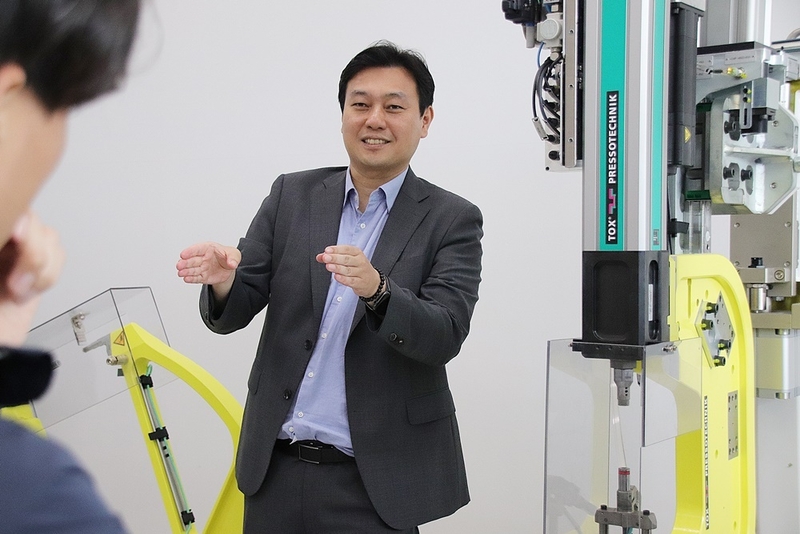
‘가전·자동차·이차전지 적용’ 클린칭·SPR·심스태킹 등 기계식 접합기술 선보여
기술 이론 교육부터 데모 시연까지 프로그램 진행
고도화된 제조기술은 제품의 경쟁력을 확보함과 동시에 원가절감·생산성 향상·품질 개선·노동 환경 제고 등 다양한 이점을 제조 산업에 제공한다. 제조기술의 발전은 제조 인프라뿐만 아니라 제조 영역 자체를 변혁시킬 수 있는 힘을 제공한다.
수차례 산업혁명을 거치는 와중에도 산업 안에서 과거·현재·미래를 잇는 제조기술이 있다. 바로 물체 간 연결 및 융합을 담당하는 접합기술이다. 이 기술은 산업이 고차원화되고 기술 집적도가 높아질수록 점점 더 요구되는 요소다. 특히 고도의 기술이 수반되는 산업 및 분야에서 더욱 존재감을 발휘하고 있다.
그중 금속 간 융합을 담당하는 접합기술은 크게 고열 방식의 ‘용접’과 일정 힘을 가하는 ‘기계 접합’으로 구분된다. 이 가운데 기계 접합은 고열·유해가스·폭발 등을 유발하는 용접 방식을 대체하는 기술로, 이미 오랜 기간 미국·유럽 등지에서 활약하고 있다.
기계식 접합 솔루션 업체 톡스프레스테크닉(이하 톡스)는 독일 규격시험인증 ‘DIN 8593’ 기반 다양한 기계 접합 기술 및 장비를 구축했다. 모든 접합공정은 품질이 최우선이기 때문에 톡스는 고품질의 접합 결과물을 제공하는 솔루션을 강조한다. 현재 가전·자동차·이차전지 등 제조공정에 기술을 공급하는 중이다.
이달 22일 경기 화성시 동탄에서 톡스 기술 시연회가 열렸다. 이 자리에는 김훈석 톡스코리아 대표이사를 비롯해 다양한 분야 관계자가 참석해 기계 접합 기술을 공유했다.
김 대표이사는 환영사에서 “전동화 시대가 개막함에 따라 그 대표주자인 전기자동차에 톡스의 기계 접합 솔루션이 이식되는 중”이라며 “경량화된 알루미늄 소재를 활용하는 사례가 늘어나는 만큼 더욱 높은 차원의 기계 접합기술이 필요할 것”이라고 말했다.
톡스는 이와 관련한 기계 접합기술을 자체적으로 보유했다. 이는 클린칭(Clinching),SPR(Self Piercing Rivet)·심스태킹(SeamStaking) 등 기술이 대표적이다.
이 중 클링칭은 상부에 위치한 펀치(Punch)와 하부 다이(Die) 사이에 각종 소재를 넣고 위아래로 압착해 소성변형을 유도하는 방식이다. 금속·연성 소재, 동종·이종 두께 등 다양한 사례에 적용 가능하다. 최성욱 톡스 대리는 “특정 자동차 차체 부위에는 접착제와 클린칭을 함께 접목해 활용하는 공정을 진행하기도 한다”고 언급했다.
톡스 클린칭 장비는 공용 툴을 이용하기 때문에 툴을 교환하는 과정을 생략할 수 있다. 또 툴 체킹 기능이 탑재돼 소재가 없는 상태에서 툴을 점검할 수 있고, 높은 동적 강도를 통해 스폿 용접(Spot Welding) 대비 일정한 강도를 유지한다. 아울러 톡스 클린칭 장비에는 알루미늄이 융착되는 것을 방지하기 위한 오일 분사 옵션이 갖춰져있어 한 차원 높은 결과물을 도출할 수 있다.
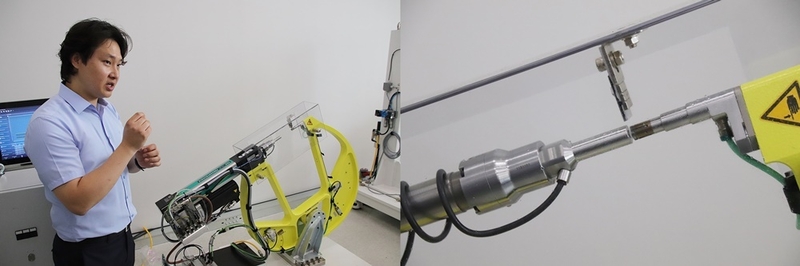
클린칭 장비는 컨트롤러, 건(툴), 품질관리를 위한 모니터 등으로 구성됐다. 특히 품질관리 시스템은 경량 프레임 특성상 필연적인 변형을 방지하는 데 기여한다. 관련 PLC(Programmable Logic Controller)을 통해 제품의 강도 및 품질을 일정하게 유지한다.
톡스는 이 과정에서 PLC를 국산화했고, 직관적 소프트웨어를 구축해 위젯 기반 사용자 맞춤형 시스템을 완성했다. 이를 통해 하나의 컨트롤러가 여러 공정에서 활용 가능하도록 하는 모듈화된 컨트롤러 구성이 가능하다. 아울러 펀치 스트리퍼(Punch Stripper), 건, 서보 모터, 등 방향을 자유롭게 설정할 수 있는 바이오닉 C-프레임(BIONIC C-FRAME)도 새롭게 구축해 운용 유연성을 확보했다.
현재 후드(Hood)·펜더(Fender)·스티어링 엘리먼트·배터리 케이스 등 자동차 공정에서 활약 중이다. 여기에 확장된 e클링칭(eClinching) 기술은 전기전도성을 극대화해 전기자동차에 특화된 기술이다. 레이저를 조사해 소재를 연질화한 후 클린칭 기술을 활용하는 레이저 클린칭 기술도 함께 구성돼 있다.
클린칭 기술에서 파생된 클린칭 볼트&너트 장비는 볼트와 너트가 융합된 부품을 소재에 압입해 접합하는 방식을 채택한다. 로봇 시스템을 차용하지 않고 수작업으로 공정이 진행된다는 점이 클린칭 기술과의 차이점이다. 그렇기에 클린칭 장비 대비 정밀하고 안정적인 제품이 도출된다. 또 일정한 힘만을 요구하기 때문에 서보 프레스를 장착하는 클린칭 장비의 설계와 다르다.
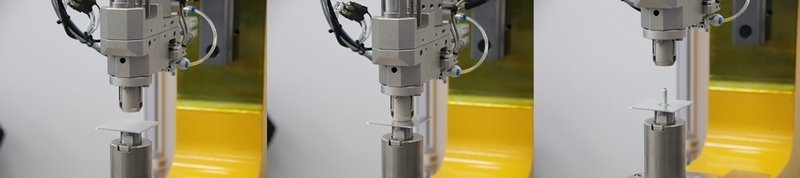
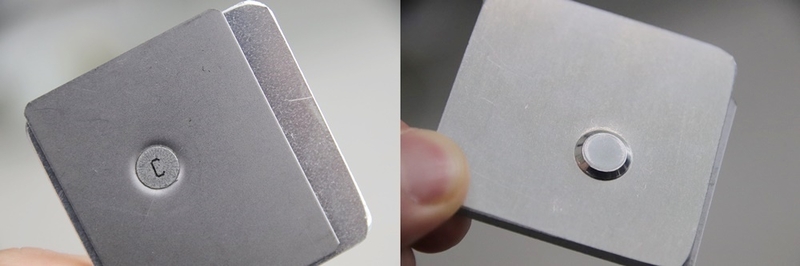
해당 장비는 공급기 안정성을 확보하기 위해 하드웨어 툴 설계데이터를 기반으로 가동된다. 클린칭을 비롯해 소재에 구멍을 뚫는 피어싱(Piercing), 리벳(Rivet)을 활용한 리벳팅(Reveting) 방식으로 공정 방식이 세분화됐다.
이어 또 다른 접합기술 SPR은 금속 소재를 접합하는 데 통용되는 금속 핀 형태의 리벳을 압입한다는 것이 클링칭과의 가장 큰 차이점이다. 톡스 SPR 장비는 각종 글로벌 리벳 제조사의 제품을 호환하도록 설계됐다. 더불어 클린칭 장비에도 적용된 툴 체크 기능이 이식됐는데, 이 장비에는 리벳이 안정적으로 압입되는지 모니터링하는 기능이 내재화됐다.
SPR 장비는 본체와 SPR 피더로 구성됐다. 이 중 SPR 피더는 리벳을 본체에 공급하는 역할을 하는데, 각 공정에 적합한 리벳 사이즈 데이터를 사전에 입력한 후 알맞은 리벳이 공정에 투입되도록 피더 자체에서 각종 리벳을 분류한다.
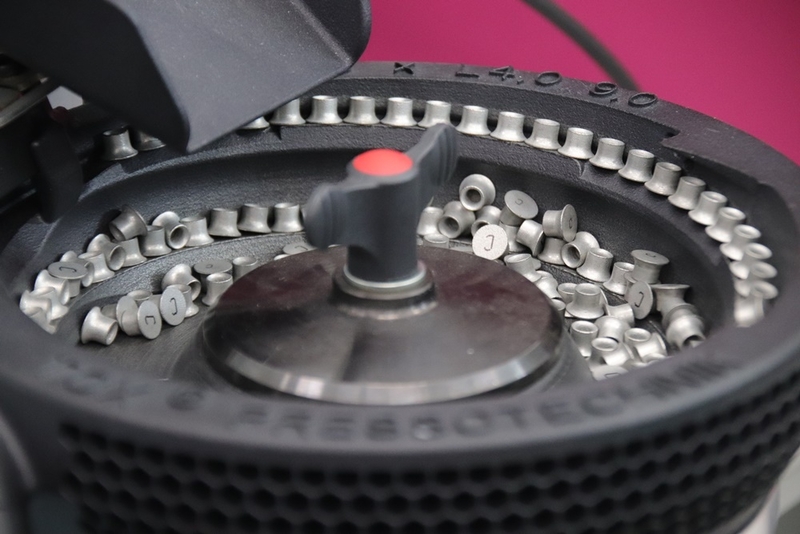
이 SPR 장비는 로봇 형태로 설계됐기 때문에 자율적인 움직임을 위해 도킹 스테이션이 필수로 장착된다. 톡스 관계자에 따르면 SPR 피더에서 이동한 리벳이 도킹 스테이션 내 매거진 탄창에 머무르고, SPR 장비가 필요에 따라 리벳을 탄창에서 충전해 활용하는 형태로 디자인됐다.
해당 장비의 가장 큰 특징은 본체 하부 다이에서 리벳을 제공하는 점이다. 톡스는 이 설계에 대한 특허를 보유했는데, 구동부에서 리벳을 공급하는 기존 모델 대비 제품 변형에 강하다는 강점이 있다. 다시 말해 다이에서 리벳을 공급하고, 구동부에서 가압함과 동시에 장비에 장착된 실린더가 장비 전체를 들어 올려 제품 변형을 최소화한다. 하부에서 리벳을 공급하는 설계의 또 다른 장점은 유연하게 장비를 배치할 수 있다는 점이다.
끝으로 톡스의 심스태킹 기술은 문·후드·트렁크 등 자동차 등 헤밍 프레스(Hemming Press) 공정에 주로 도입돼있다. 헤밍 프레스 공정은 외판 패널과 내판 패널을 포개는 과정으로, 심스태킹 공법은 이 과정에서 양 판에 발린 본드가 마르기까지 접합을 잠시 돕는 가접 방식이다.
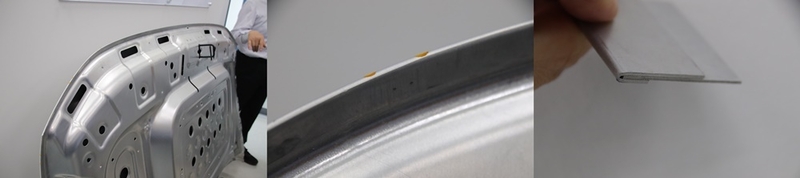
최성욱 대리는 “기존 헤밍 프레스 공정에 활용된 가접 방식은 환경 및 품질 문제를 안고 있었지만, 심스태킹 공법은 이를 해결하면서도 소재 변형을 최소화한다”고 강조했다.
한편, 이날 시연회는 톡스의 각종 접합 공법과 솔루션, 제품을 직접 체험하는 프로그램도 함께 진행돼 참관객의 이해를 도왔다.
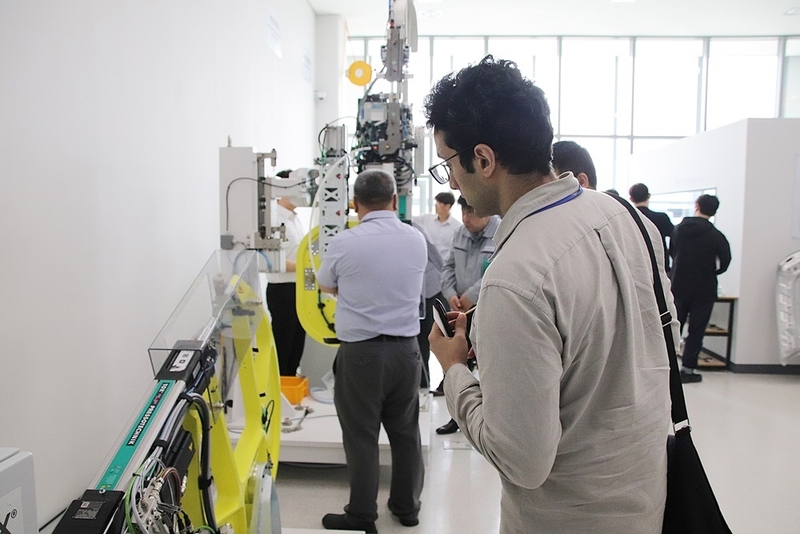
헬로티 최재규 기자 |